Article: 2024.08.28_MTRJ002-PIONEER SHIPPING SCHEDULED TO SEPTEMBER 10TH
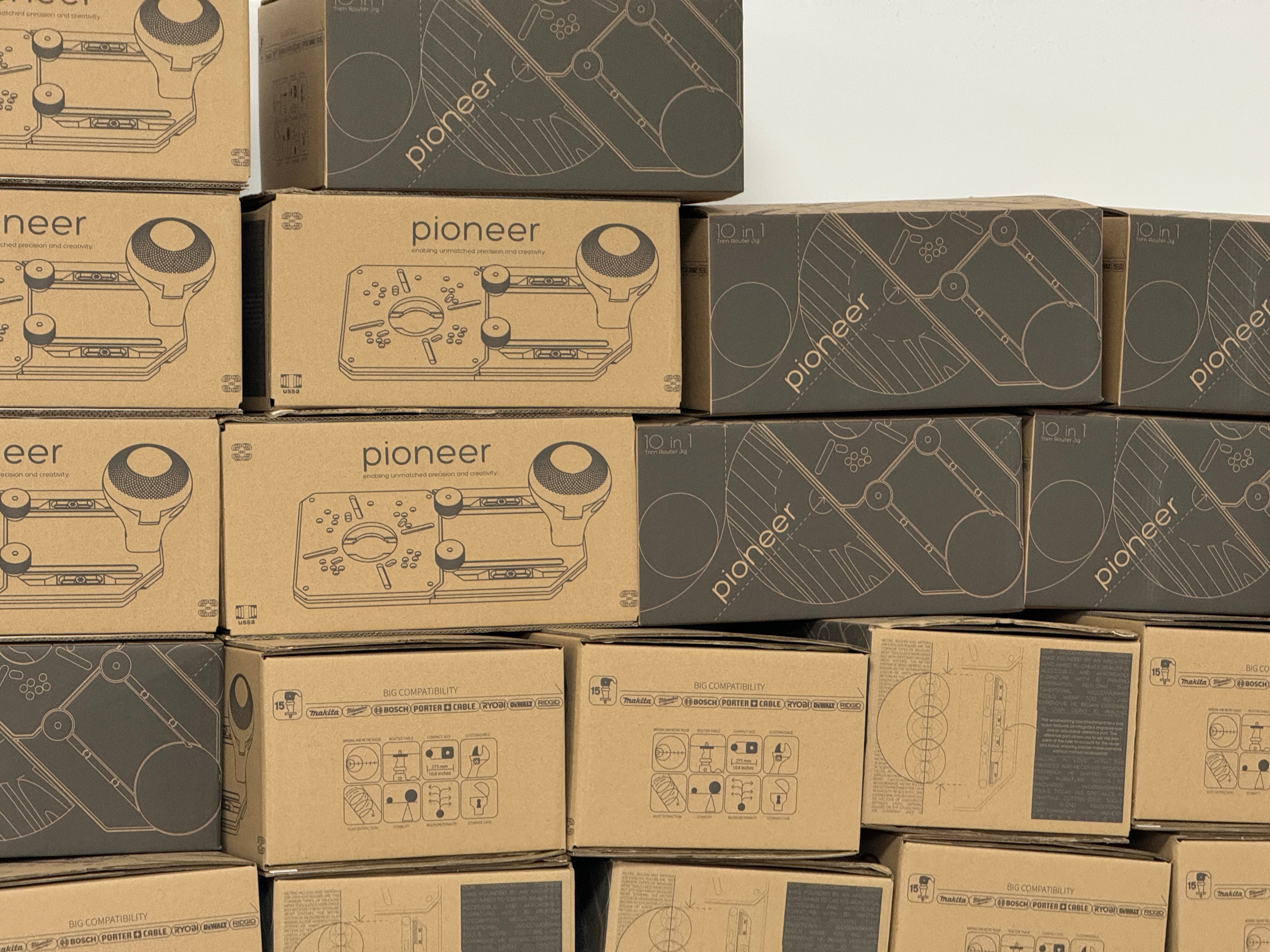
2024.08.28_MTRJ002-PIONEER SHIPPING SCHEDULED TO SEPTEMBER 10TH
Assembly Challenges:
As mentioned in the previous update, CNC manufacturing was initially scheduled to be completed by August 8th, with assembly expected to take two days. We anticipated that everything would be ready for shipment by August 13th. However, here’s what went wrong:
Problem 1: Surface Finish – August 8th
The aluminum parts were made from 6mm stock aluminum plates, which came with a factory brush finish on their surface. Since the parts were exactly 6mm thick, the stock material was used directly without any additional surface treatment. Unfortunately, sandblasting and anodizing were insufficient to achieve a smooth finish, leaving the factory brush marks visible. This not only caused an unpleasant sound when the bottom plate was moved but also resulted in an unsatisfactory aesthetic appearance.
Cause:
The manufacturer overlooked previous feedback and did not address this issue in the earlier prototypes.
Solution:
The manufacturer had to send all parts back to the anodizing department to remove the anodizing layer. Each part was then manually brushed before being sent back for a second round of anodizing.
Result:
This process resulted in a 5-day delay.
Problem 2: Assembly Complications – August 13th (450 kg of Hardware)
The CNC manufacturer had agreed to handle the assembly process, promising that it would take two days with a team of 10 people working daily. On August 14th, I arrived at the factory after having previously sent all parts for assembly from 14 different manufacturers. These included laser-cutting, printshop, nylon cases, hardware, injection molding, accessories, etc. Upon receiving 450 kg of hardware and over 50 boxes of nylon cases, the factory manager was shocked by the scope of the task, realizing that the complexity of the process had been underestimated.
The first two days were spent sorting the hardware into smaller boxes, attaching knobs to the edge guides, and assembling the basic geometry of the jig itself—200 pieces out of the 1,500.
Cause:
This issue arose from my miscommunication with the factory manager. I relied too heavily on his personal experience instead of clearly explaining each step of the assembly process, calculating the total required time, dividing it by working hours, and providing an exact schedule for the assembly.
Solution:
Despite the initial shock, the responsible manager took on the assembly task regardless of the time required. I personally stayed at the factory, overseeing and explaining every step of the process for the first nine days until we reached the final stage.
Result:
This led to a significant waste of time and resources.
Problem 3: Engraving Mistake – August 14th
Upon inspecting the parts on my first day at the factory, I discovered that the engraving on the bottom plate was from the previous model instead of the current one. By this time, 700 units had already been engraved, meaning these parts had to undergo the same surface finish correction process: re-anodizing, manual brushing, re-anodizing again, and then sent back for new engraving.
In addition to this mistake, the engraving of the ruler was incorrect and out of scale, forcing us to find a new engraving manufacturer in a very short period.
Cause:
The manufacturer decided to switch engraving shops at the last minute for personal reasons, which led to misunderstandings in the documentation. Despite my repeated emphasis on the complexity and importance of the ruler engraving, the manufacturer failed to give it the necessary attention, even though I had personally engraved 500 units with the previous manufacturer.
Solution:
A high-end engraving shop was hired on short notice, which significantly increased the cost—tripling the price compared to the previous one.
Result:
This caused a partial delay in the assembly process, potentially extending the timeline by up to two weeks.
Problem 4: Dirt and Scratches on Parts – August 15th
While inspecting the router holder part of the jig (a black square part), I noticed that 80% of the parts had surface finish issues, including scratches and water marks.
Solution:
The factory workers had to evaluate the entire production batch, select the good parts, and send the rest back to the anodizing department for the same process: de-anodizing with sandblasting, manual brushing, and re-anodizing.
Cause:
The CNC manufacturer’s staff failed to check the anodized parts thoroughly and did not implement strict quality control with the anodizing department.
Result:
This led to a partial delay in the assembly process, requiring up to 13 days to fully resolve the issue.
Current Status:
As of today, approximately 600 units have been completed, assembled, and are ready for shipping. The remaining 900 units are expected to be ready for shipment by September 10th.
Thank you very much for your patience, understanding, and continued support.
22 comments
I am with Grant on this one. Can’t wait to hold it in my hands, but haven’t gotten any updates regarding shipping or updated order status in weeks… I am willing to wait if I get an update, but the more time passes by, I am getting more nervous…
Roman
Hi there
Just wandering if there is some sort of shipping schedule or expected eta. At this stage I am not exactly sure if something has gone wrong with my shipment. Your feedback will be much appreciated
Grant
I’ve received mine, minutes ago, only had time to open it up and I’m very very happy with the product I received: it’s absolutely beautiful!
thanks for the hard work you put in it.
now, time to play with my new toy…
vince
My problem with my order tracking number has been resolved successfully.
Oleksandr Busarov
Gentlemen,
did they send you an order with a tracking number?
I am trying to find out if my order has been sent to me.
Unfortunately, all my letters have remained unanswered.
When I ordered, I was promised delivery the next day after payment….
6 days have already passed.
Very strange.
Oleksandr Busarov
I received my order last week and have had some time to play around with the jig. I’m so excited to really spend some time using this thing. The machining and manufacturing is very high quality. I’m thankful for all the time and effort you put into designing and manufacturing the jig. Top Notch!! That said, I also didn’t receive a copy of the physical manual. It would be great if there were a way to get that at some point. I know you’re in the process of making a new one, so I can understand not wanting to include the out-of-date version. I’m not upset about it though. I’m too excited about the actual jig! Thank you!
Jared McEntaffer
Jason Davis
Jason Davis
발송이 되었나요
yondong Cho
I just received my package! I only opened it for a few seconds, but I could already tell how well-made it is. Thank you! It has exceeded my expectations, and it will be a joy to own.
Location: US
Vito
I received the tool set today and am excited to get started, I just re-watched the promotional video and it obvious that the product shipped is a upgrade from what I was first expecting.
I do have one question about the booklet that was depicted in the video as it was not in the delivered package. Is this a problem that you are aware of?
I could really use instructions in the printed format please advise.
Bryan
How do I update my shipping address? It has changed since I placed my order. Thx.
HDB
Hi,
I wrote you several letters.
Unfortunately I did not receive an answer.
In my opinion, this is very strange.
I will repeat my question. How quickly will you send the Pioneer order after payment?
I hope for your understanding.
Regards Oleksandr
Oleksandr Busarov
Hi. Have you shipped my order?
Tom
Thanks a lot for all the info you have provided so far. It is unbelievable and very admirable how much effort,sweat and dedication you have put in this project so far. I truly believe what you create is extraordinary. Wishing you the very best as you get closer to the shipping date – I can’t wait to see this amazing product in action! Martin from Czechia.
Martin
What a ride! I appreciate this detailed explaination very much, thank you! Good luck with all the headaches, you will come out a stronger product developer in the end 💪. Looking forward to receive the jig, when the time comes. Good luck! All the best from the Netherlands
Arnoud
Hi,
who will receive the first batch of 600 units ? Did you send it first ordered, first sender or by destination ?
Jerome
I honestly don’t mind waiting a little bit more as I can see you’re putting your name to this product and you wanna guarantee for the rest of us a product up to your standards
Gavin Robinson
Thanks for feedback.
Be patient I will continue to encouraged you.
First product will always a pain walk. It will be better next time, maybe with less surprises !!
The first pieces seem amazing….
Regards
Gilbert Nicolas
Wow, what a nightmare! As someone who works in product design/manufacturing, I understand this process. What I have learned over the years is to over-communicate every single detail about your product. These factories are looking for the cheapest sub-factories and labor which, are not the best at executing the details needed to get the job done.
Herman
I appreciate the attention to details and the will to deliver a no compromise product. I’ve high hopes and high expectations regarding this jig and I’d rather wait a few more weeks than receive something with a lower quality level. Thanks for the updates
Vince
The amount of time, sweat, and frustration that you have poured into this makes me appreciate this product even more. The image of the jigs already packaged looks amazing and the attention to detail seems immaculate.
Mark
Leave a comment
This site is protected by hCaptcha and the hCaptcha Privacy Policy and Terms of Service apply.